The quality of OFC connectors directly affects network speed, signal attenuation, insertion loss, reflection loss and other aspects. High-quality fiber connector can provide higher transmission rates, lower insertion loss and reflection loss, thereby ensuring the reliability and efficiency of network transmission.
All OFC cable connector of Yingda strictly comply with IEC standards, Telcordia and other standards for strict production and testing, and can only be shipped after 100% qualification. Combining production practice with the latest industry standards, Yingda recommend buyers, please pay attention to the optical performance, mechanical reliability and process standards if you wanna buy the best OFC connectors.
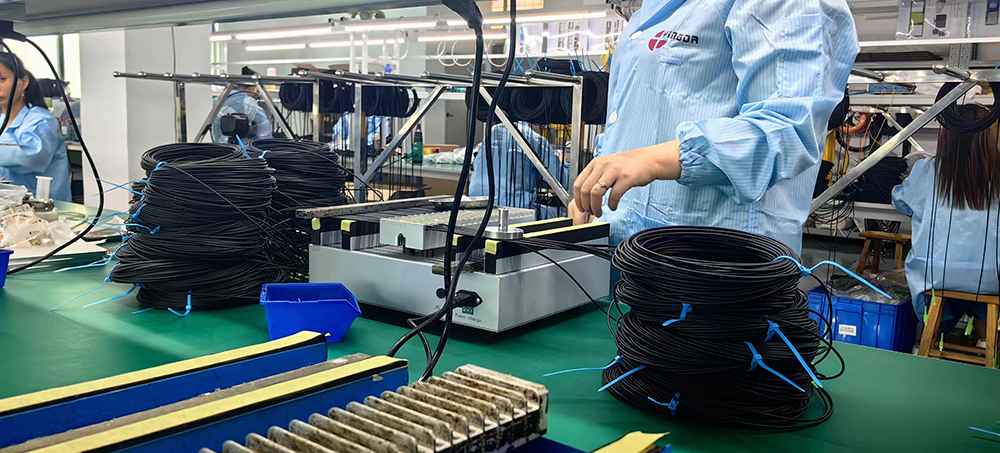
1. Core indicators of connector optical performance: insertion loss and return loss
Insertion loss (IL)
- For single mode fiber connectors: ≤0.35dB (IEC 61755-331:2024 standard @1310nm wavelength)
- Multimode fibre connector: ≤0.5dB (@850nm window)
Return loss (RL)
End face type | Application scenario | Minimum standard | Test method |
APC (green) | 5G fronthaul, broadcasting | ≥65dB | OTDR bidirectional scanning (sampling density 1000 points/m) |
UPC (blue) | Data center | ≥50dB | OTDR bidirectional scanning (sampling density 1000 points/m) |
PC (blue) | Low-speed short-distance transmission | ≥40dB | Light source + optical power meter combination test |
Acceptance method: During the factory production process, there will be a desktop insertion loss and return loss tester for precise testing. Only fiber optic ends that meet the loss requirements can enter the next procedure. If the customer receives the product, an optical power meter can be used for bidirectional testing. The deviation must be <±0.05dB to be qualified.
2. Mechanical reliability verification
This mainly include the plug-in durability of the fiber optics connector, after how many times will the loss suddenly increase or physical deformation or damage, and if possible, can request to do humidity and heat tests and smoke tests.
Plug-in durability
- Conventional plug-in: After 500 times (force 20N±10%), IL change ≤0.1dB
- Hot plug test: -40℃~85℃ cycle 100 times, no physical deformation of the connector
Environmental adaptability
- Humidity and heat test: 85℃/85%RH environment 1000 hours, contact resistance change ≤3mΩ (gold plating layer ≥0.2μm)
- Salt spray corrosion: 5% NaCl spray 96 hours, oxidation area ≤0.5%
- End face process parameters
For customers with high quality requirements, our company will use 3D interferometer to test the fiber end face for each connector, patch cable or pigtails, mainly three aspects: curvature radius, vertex offset and fiber sag amount. Every fiber optic termination kit can be equipped with an independent 3D test report.
Parameters | Qualified range | Detection equipment | Impact |
Radius of curvature (ROC) | 7-25mm | White light interferometer | <7mm increases contact pressure and causes fragmentation |
Apex offset (Apex) | ≤50μm | 3D interferometer | >50μm causes air gap and increases insertion loss |
Fiber sag | >50nm | Too low causes echo reflection to exceed the standard |
4. How to avoid buying inferior connectors?
- First, we can check whether the certification reports provided by fo cable connector supplier are true or not, such as IEC 61300-3-35 (OTDR test) or IEC 61755-3-31 (insertion loss test).
- Second, fiber cable termination products that are only tested for insertion loss at room temperature (samples <10pcs) can be rejected. For harsh environments or environments with high temperature, it is recommended to include high and low temperature cycle tests. Yingda test rate is 100%.
- Third, if the supplier claims to support 0.1dB ultra-low loss, they need to provide a third-party laboratory report (such as CNAS certification), etc.
- Finally, after the construction is completed, the following three tests must be performed for project acceptance:
- OTDR test after construction, with an accuracy of ±1 meter for locating the fault point;
- Use a visual fault locator (red light pen) to check the continuity of the optical fiber;
- The batch sampling rate is ≥5%, and includes environmental stress test samples.
Conclusion
When we sourcing suppliers or test the finished products, the above methods can be flexibly applied to effectively kick out more than 90% of inferior connectors.
FAQ
What is the price of lc connector price?
LC connectors are basic fiber optic accessories, so the price is very cheap, generally between USD0.16~USD0.2. They can be delivered partially assembled or all loose parts. At the same time, when purchasing, pay attention to whether the price includes the ceramic ferrule and whether the ceramic ferrule has a ferrule holder (stem).
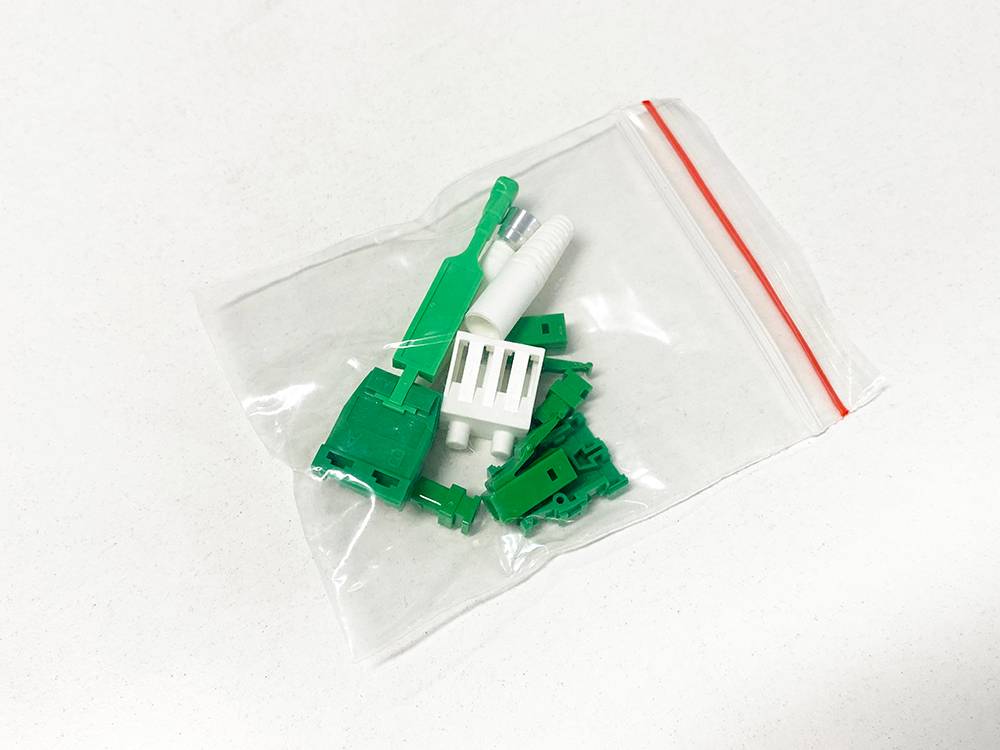
What is the difference between sc and lc connector?
LC connectors outer size is half of SC connector, with different application and connection way. For more information, please read article: What is the difference between lc and sc connector?
What is fiber optic connection?
Fiber Optic Connection refers to the technology of precisely aligning the cores of two optical fibers through physical means to achieve efficient transmission of optical signals. For how to connect optical fibers, please refer to the article: What are the fiber termination methods for optical fibers?
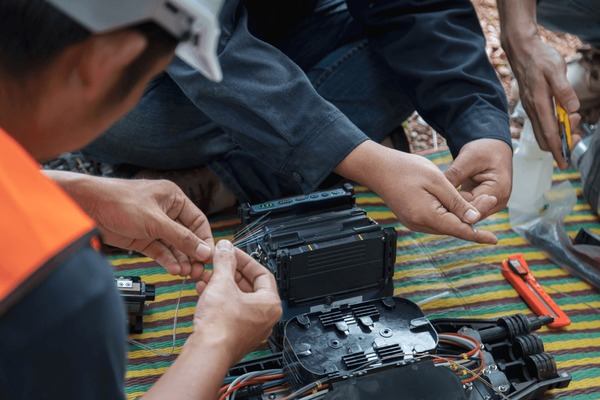
What is lc connector?
LC Connector is a miniaturized fiber optic connector developed by Bell Labs. It uses a 1.25mm ceramic ferrule and is only half the size of a traditional SC FC connector. It belongs to the small form factor standards for high-density wiring.
How to clean lc fiber connectors?
If you use a patch cord or pigtails on site construction, please clean the LC connector with a one click cleaner pen, cleaning cassette or dust free paper, it will be the best way to do.
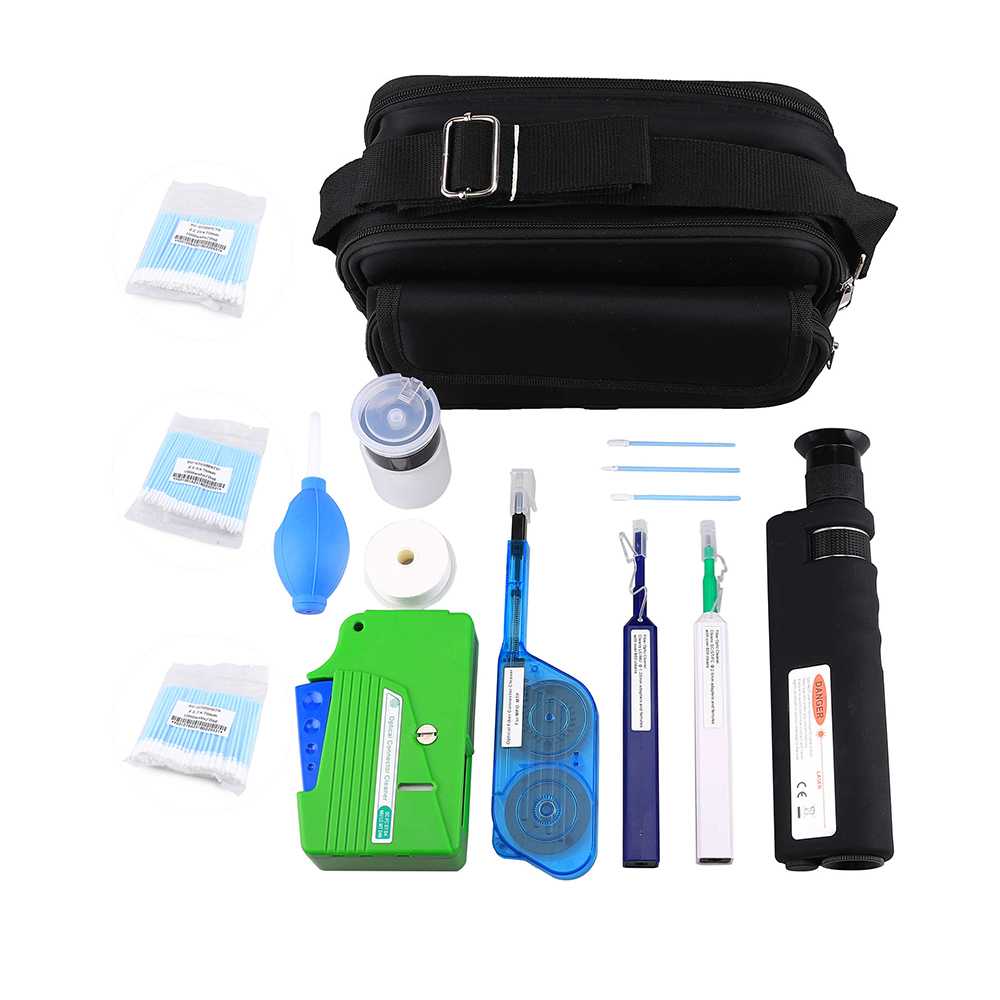
Buy fiber optic cleaning tool kits from Yingda
What are the polishing methods for optical fiber connectors?
The polishing methods for optical fiber connectors mainly include UPC, PC, SPC, and APC. For details, read more here:Optical Fiber End Face Grinding Polishing Method PC UPC APC
What operations of fibre optic connectors are improper?
- Touching with fingers will leave residual grease and cause signal attenuation;
- overload bending will cause internal fiber breakage and cause signal instability;
- Chlorine-containing or corrosive cleaners will permanently damage the ceramic ferrule, so they must not be used;
- Not wearing a dust cap during use, leaving the fiber end face exposed to the air, etc.
All above operations will cause damage to the connector or excessive loss that affects signal transmission.
How often to clean optic cable connectors?
For home use or office networks, recommended to clean and inspect once every 6 months. If use in data center/industrial environment, recommended to clean it every quarter + monthly microscope inspection to ensure stable transmission. Article “the importance of regular cleaning and maintenance of fiber optic patch cords” may help you more.