From the article “How to judge the quality of fiber optic connectors”, we can know that the quality of fiber connector depends on insertion loss, return loss, plug-in and pull-out times, fiber end face 3D parameters, mechanical reliability, etc. According to statistical surveys, mechanical factors cause up to 68% of fiber link failures, far exceeding the impact of optical performance. The core performance indicators of fiber connectors directly determine the stability and life of the communication system.
What are the general types of mechanical reliability failures?
- Fiber connectors with insufficient plug-in life are prone to poor contact, causing optical signal interruption or attenuation (e.g. LC connectors need to withstand ≥500 plug-in and pull-out times);
- Mechanical vibration in industrial scenarios may cause unreinforced fiber connectors to move >50μm, resulting in microbending losses (≥0.5dB);
- Abnormal contact stress when the radius of curvature is <7mm may cause the ferrule to break (loss >30dB), resulting in permanent optical path interruption;
- Ultraviolet, chemical corrosion of the optical fiber connector housing accelerates material degradation and aging, and also causes water vapor intrusion, which causes a surge in optical fiber attenuation, etc.
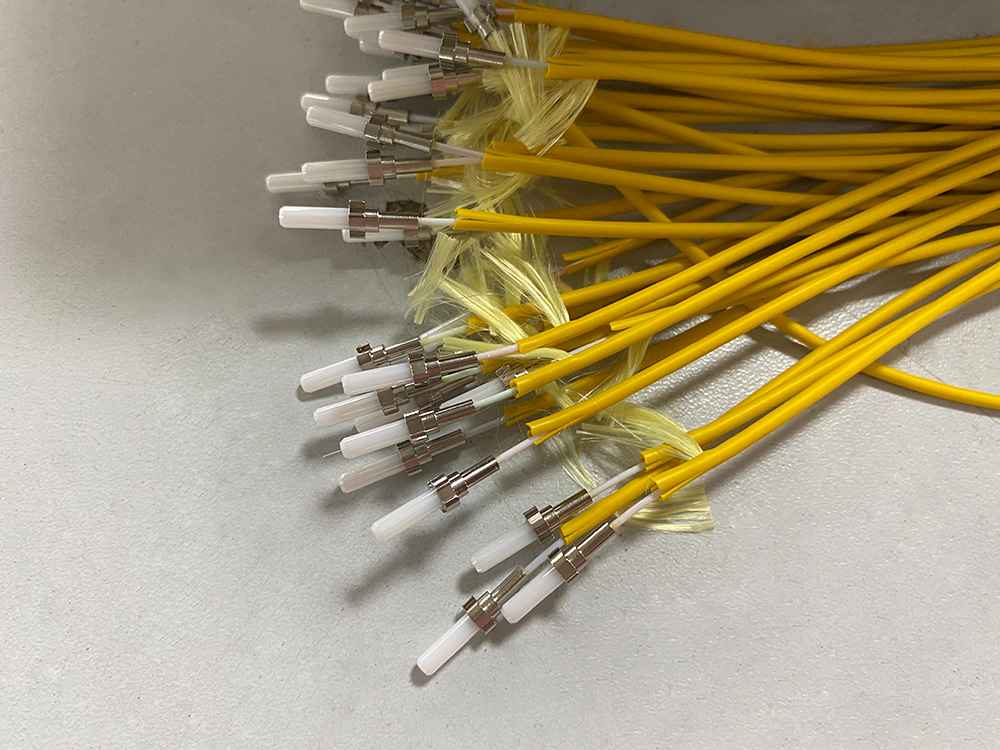
How to improve the mechanical reliability of fiber connections?
In order to improve the mechanical reliability of fiber optic cable ends, our company follows international standards from procurement, production, testing, packaging, and logistics, refines each link, and strictly implements it 100%.
- 1. Use high-quality fiber to fiber connector parts, lc connector ferrule and optical cables, and never use second-hand or inferior raw materials. All products are made of new materials to ensure high quality from the source.
- 2. All lc and sc fiber are made of high-quality fibers MADE IN CHINA or brand Draka, Fujikura, AFL, or Corning to ensure that the bending radius and 3D parameters fully meet customer needs.
- 3. All equipment, tester, fiber optic termination tools and curing glue used in all production processes are world-class brands to ensure stable and reliable product quality.
- 4. All details of the cable structure, fiber reinforcement core, metal parts, loose tube, etc. must be verified with the customer firstly before order and produced strictly in accordance with the order requirements, and pay much attention to the short-term and long-term tension requirements.
- 5. All product packaging and winding coil number are also strictly implemented in accordance with international standards to ensure that all optical connectors have good anti-vibration protection after delivery.
- 6. For harsh environments or sensitive temperature change applications, Yingda will do high and low temperature cycle tests in factory to prevent material aging and cracking.
Fiber connector mechanical reliability test methods
There are many methods to test the sc lc fiber connector mechanical reliability, and hereafter Yingda introduce the way how we do.
1. Core physical performance test
Plug-in life test
- Method: Simulate the actual plug-in action, apply 20N±10% force to repeatedly dock the fiber connector
- Standard: Insertion loss change≤0.1dB after≥500 times (industrial grade requires≥1000 times)
- Equipment: Automatic plug-in test machine (precisely control force and speed)
Vibration reliability verification
- Three-axis vibration test: frequency 5-2000Hz, acceleration 10G, lasting 2 hours
- Qualified judgment: no optical signal disconnection, insertion loss fluctuation ≤0.2dB
- Application scenario: required test items in dynamic environments such as vehicles and aviation
Mechanical shock test
- Condition: half-sine wave shock, peak acceleration 300G, lasting 6ms
- Failure characteristics: optical connector shell cracking or ceramic ferrule fragmentation (microscope inspection required)
2. Environmental adaptability test
Test type | Test conditions | Acceptance criteria |
High and low temperature cycle | -40℃↔85℃, 100 cycles | No structural deformation, insertion loss change ≤0.15dB |
Wet and hot aging | 85℃/85%RH, 1000 hours | Oxidation area of metal parts ≤0.3% |
Salt spray corrosion | 5% NaCl solution spray, 96 hours | Contact resistance change ≤3mΩ |
Note: The new version of YD/T 1272 standard has canceled the drop test and strengthened the fiber optic connector tail tensile test.
3. Special tests on end faces and structures
Tail tensile test: Apply xxKN tensile force along the fiber axis for 1 minute until the fiber cable break or the glue layer cracks, and see how much tensile force it can withstand.
Tension Test 1: Unitube Drop cable with Metal SC Connector
The maximum tension strength (breaking load) can reach up to 120N for 1 minutes without breaking, good enough for indoor wiring, duct pulling request.
Tension Test 2: Figure 8 cable with SC Connector
The maximum tension strength (breaking load) can reach up to 116N for 1min without breaking.
Bending stress test
Bend the lc fiber connector to a radius of R=40mm, cycle 100 times, and monitor the maximum stress in the range of ≤0.3dB when increase the fiber microbending loss.
End face integrity inspection
- Equipment: 400x fiber microscope or 3D interferometer
- Key parameters: Scratch length <20um, pit diameter <5um
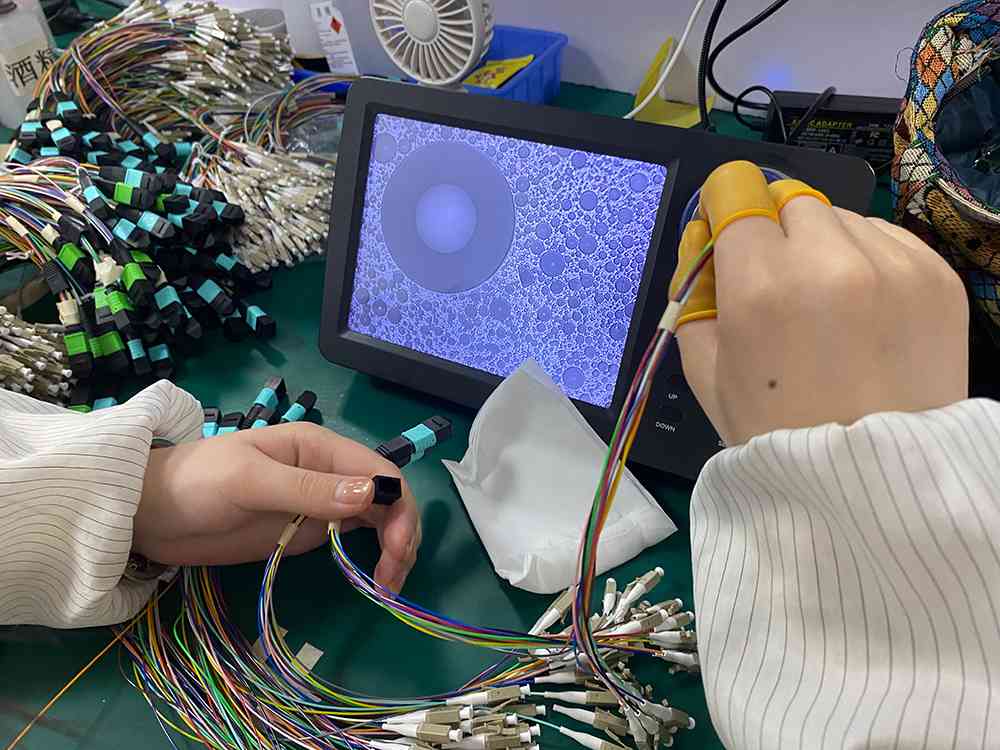